Supply chain in control with coronavirus
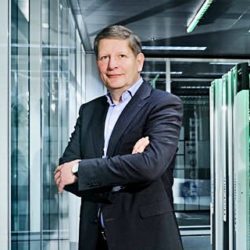
Slowly but surely, everyone is realizing that supplies from China are stagnating as a result of the coronavirus outbreak. Containers are stuck at the ports in Hong Kong and Shanghai. And factories have temporarily shut down. So how is coronavirus impacting on business life and supply chain in particular?
The impending coronavirus pandemic is not only affecting factories across the board in China. It also impacts freight flows by air, sea and rail. When the supply chain grinds to a halt, customers will have to jostle for priority. Due to the resulting material shortages, we are likely to continue to feel the impact of Covid-19 for several months.
During the outbreak of the SARS epidemic in 2003, I was an expat in Taiwan. The staff of all departments in the affected areas, which included Donguan as well as Taiwan, were divided into three groups. The groups worked in rotation – two from the office (in separate buildings) and one from home. Luckily we were fine and none of us caught the virus. But with every trip to a local store our minds were full of how to minimize the risk of infection.
Buyers working overtime due to coronavirus
Any company with suppliers in China is now largely in the dark regarding which deliveries will arrive when. Buyers are working overtime trying to gain insight into the supply chain. But they are no match for the sheer number of suppliers to monitor and the ever-changing dynamics surrounding most shipments.
It will be necessary to reassess the availability of components to make new production and/or delivery schedules. Despite much shuffling of orders and stock, the sales department will probably have to disappoint customers multiple times, which will ultimately put pressure on sales performance.
Most supply chain management systems will fall short. They depend on reliable, periodic (often weekly) updates that are no longer being provided, because the majority of the people in China are off work.
Control tower
In a crisis situation like this, it is necessary to use the internet to connect the various supply chain information systems together. That creates a basic control tower, which reveals which problems the company should tackle first. If multiple containers are stuck at a port or airport, for example, the company could choose to pay more to fast-track a particular container carrying parts for high-priority orders.
For instance, Hewlett Packard Enterprise’s control tower can monitor customer orders dynamically through the supply chain. This enables the company to significantly improve its delivery reliability and even reduce the lead time by half.
The current Covid-19 situation once again underlines how important it is to have good agency representation in China. The top management has to travel to the country – as soon as it becomes possible again – to stabilize the business situation… and above all to build strong relationships with key suppliers.
Jan Roodenburg was previously responsible for the supply chain of Hewlett Packard Enterprise EMEA and of Philips Multi Media Systems based out of Taiwan.