Rising supply chain risks make a Plan B essential
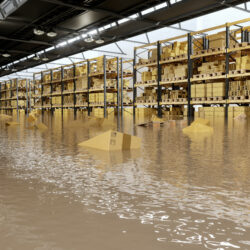
How can you build a supply chain that is less affected by disruptions such as wildfires, flooding and drought? AIMMS decided to combine its supply chain network design software with Royal HaskoningDHV’s knowledge of site-specific risks. During a recent Webinar Wednesday, they both explained how this allows companies to calculate the impact of such risks and draw up a Plan B. “Many businesses underestimate the indirect impact of these hazards on their supply chains.”
By Marcel te Lindert
Once upon a time, supply chain network design was all about cost savings; companies tried to develop a supply chain that enabled them to compete on cost. Over time, as they realized that cost savings were often at the expense of stock availability, the service level became an important optimization factor. “But what are CEOs talking about today? Sustainability and risk,” claimed Paul van Nierop.
Van Nierop is Product Owner Supply Chain at AIMMS, a Dutch provider of supply chain network design software. He has a lot of contact with internationally active companies and supply chain experts, and has noticed that the rising supply chain risks are keeping CEOs awake at night. “We currently live in an uncertain and unpredictable world. The number of disruptions in our supply chains is increasing. More and more companies are deciding to redesign their supply chains, and reducing risk is a key reason for this.”
Weather versus climate
Royal HaskoningDHV has an extensive database that identifies the risks for each location. Those risks may be due to geopolitical issues such as developments in Ukraine and the Middle East, but also due to weather or climate. “Those two are not the same,” emphasized Daniel Martens, Climate Risk Intelligence Lead at Royal HaskoningDHV. “Weather phenomena such as hurricanes and floods cause disruptions on a daily basis, and are due to short-term changes in the atmosphere. Climate change is about long-term changes, such as the increasing dryness in certain parts of the world.”
Martens showed images of wildfires, landslides, floods and droughts. “The indirect consequences of these hazards on our supply chains are often underestimated. For example, how will the increasing heat stress affect our future productivity? Many people don’t realize that prolonged periods of high temperatures can damage infrastructure such as railways. Or think of key waterways such as the Rhine and Yangtze, which last year were barely navigable for a lengthy period due to low water levels.”
More risk awareness
Martens acknowledged that supply chain professionals can feel overwhelmed by the multitude of hazards that can result from weather events, climate change or other phenomena such as earthquakes. “As Royal HaskoningDHV, we can help raise awareness within companies. In doing so, we distinguish between transitional risks and physical risks. Physical risks include acute risks such as storms and heat effects as well as chronic risks such as sea level rise. Transitional risks are things like geopolitical and economic risks.” All those risks can impact companies’ supply chains, both directly and indirectly.
“Subsequently, we address the question of how companies can guard against these risks. We see that most companies are trying to reduce their own impact on the climate, such as by minimizing carbon emissions. But they often pay less attention to what they can do to adapt their own supply chain and make it more resilient.”
Database integrated with AIMMS software
Martens gave an example of how Royal HaskoningDHV performs a quick scan for companies. Based on its database of site-specific risks, the consultancy can indicate which sites within the supply chain face the greatest risks and why. “These can be the company’s own locations such as factories and warehouses, but also supplier sites,” Martens explained. “Next, we look at the three or four sites with the greatest risks and analyse how well the factories or warehouses at those sites can withstand the risks.”
Thanks to the integration of Royal HaskoningDHV’s database with the AIMMS software, companies are able to take site-specific risks into account when redesigning their supply chains. “We map companies’ supply chains and identify the most critical locations. These can be their own factories and warehouses as well as those of key customers and suppliers. We then use Royal HaskoningDHV’s data to calculate the risk factor of those locations,” explained Van Nierop.
What is Plan B?
The software shows which geographical locations are at greatest risk. Van Nierop: “Then we start analysing scenarios, looking at these locations one by one. That shows the impact of a site being unavailable due to a fire or flooding, for example. For each scenario, we can calculate the impact on costs, service levels and emissions.”
This solution enables companies to anticipate disruptions by creating a business continuity plan. For example, what is Plan B if the distribution centre in Paris is out of action for whatever reason? Is it possible to serve all of those customers from the distribution centre in Brussels? Or do you have to make use of other distribution centres too? “Analysing different scenarios reveals the best emergency measures so that you have a Plan B ready just in case,” he stated.
Long-term view
For additional insight, there is a graph plotting the risk factor against the impact on profits. Each dot on the graph represents a site. Van Nierop: “This graph shows which locations you need to focus on. The dots at the top right of the graph represent the sites with a high probability of a high-impact disruption, so that’s what you need to work on. If it involves a distribution centre, you could look at another site. If it involves a supplier, you may have to think about multisourcing.”
Besides producing that graph for the current situation, it’s also possible to produce one for the situation 10 or 20 years in the future. This can reveal the supply chain impact of issues such as global warming and sea-level rise. Van Nierop: “You should look at the long term as well as the short term. Both are important in the context of supply chain resilience.”
You can listen to the recording of the entire webinar here.