‘Manufacturing industry must fundamentally transform to remain successful’
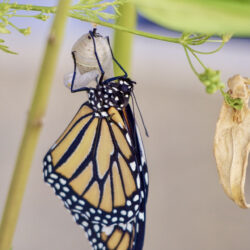
The future of the European manufacturing industry is uncertain, volatile and complex. To thrive in such an environment, manufacturers must fundamentally transform their operations to become more resilient and agile, according to Workday, a provider of enterprise cloud applications for finance and HR, and data company IDC.
Today’s manufacturers must balance costs and data security while also ensuring compliance with environmental, social and governance (ESG) regulations. To achieve this, it is essential to have the right skills and talent as the foundation for successful business transformation and sustainable long-term business growth, according to Workday.
Business challenges
Workday and IDC have identified several business challenges currently facing manufacturers. These include persistent supply chain shortages and growing competition, which increase the need for agile decision-making and operations to build greater business resilience. In addition, rising internal costs have intensified the need to monitor and control costs.
On top of this, the rising number of cyberattacks puts manufacturers at a heightened risk of factory shutdowns, not to mention the significant costs associated with resolving security breaches. Last but not least, fluctuations in demand at customer and market level require a higher degree of flexibility in both production and service.
Skills gaps
Skills gaps are impacting on business transformation and operations, Workday claims. In particular, there is a lack of professionals with the necessary digital knowhow, software engineering skills to develop smart and connected products, and cybersecurity skills to protect against attacks.
According to the software vendor, the need to quickly change requirements to operational skills results in higher scrap rates in production, thus increasing costs. Longer production cycle times and quality issues are leading to decreasing customer satisfaction and subsequently limited business growth.
To reduce or eliminate the negative impact of skills gaps as well as to avoid falling behind global competitors, manufacturers must address their workforce and talent management from end to end: from talent attraction to employee engagement, experience and retention, Workday adds.
Close internal collaboration
Close collaboration between CHROs, CIOs and COOs is essential to get the right data and generate actionable insights, Workday states. Among other things, successful skills & talent management requires understanding the skills needed and identifying gaps, understanding job/task requirements, recruiting/allocating the right skills to tasks, providing appropriate training programmes, and understanding which factors affect the employee experience.
According to research by IDC, manufacturers experience the biggest skills gaps in the ability to work with large datasets (43%) and the ability to solve problems (41%). A total of 36% of manufacturers are investing in ESG/sustainability to attract new talent, while 48% regard data privacy laws as a major investment barrier to executing employee experience initiatives.
Fundamental transformation necessary
“To address persistent supply chain shortages, increased competition, rising costs and evolving customer demands, manufacturers must undergo a fundamental transformation of their operations,” states Hette Mollema, Vice President Benelux at Workday.
“Manufacturers need to invest in attracting new talent and the required skills, improving employee experience, and enhancing operational resilience through agile and flexible workforce management and planning.” These investments, according to Mollema, lay the foundation for long-term business growth and successful transformation, allowing companies to better manage costs.