How COVID-19 vaccines turned the pharmaceutical supply chain into the ultimate gamble
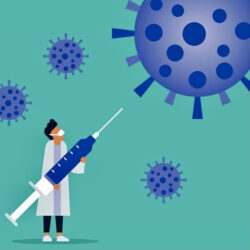
As the world races to vaccinate as many people as possible in the shortest possible time to save lives, the supply chain of pharmaceutical companies has become a very hot geopolitical battle. This is surprising for many supply chain experts because they have known since the beginning of 2020 that the supply chain was going to be one of the biggest challenges in vaccination. They also realized that ensuring a functioning supply chain required a high level of guessing when, where and how much to invest – variables never before seen in supply chain management.
By professor Carlos Cordon
The current geopolitical battle is so intense that even politicians are visiting and learning about pharmaceutical supply chains. On 19 February, a European commissioner toured a factory of an AstraZeneca supplier in Switzerland to learn about the readiness of the supply chain for the vaccine. In the USA, two consecutive presidents have used executive orders to accelerate the COVID-19 supply chain. All of those pressures were, although well intentioned, not enough to avoid delivery delays.
Since the beginning of the pandemic, pharmaceutical companies have raced to develop, test, get approval of and manufacture COVID-19 vaccines. Supply chain experts have also known since that time it would be a very bumpy road. Today, it is very difficult to evaluate if the whole effort has been a great success or a dismal failure; much depends on the definition of success or failure as well as expectations. Worse, the burning question “could we have saved more lives?” lies at the heart of the challenge.
As the pandemic started, many pharmaceutical companies and their staff were over-dedicated to developing a vaccine for COVID-19 with one single objective – to save as many lives as possible. Their only constraints were time: for the approval processes, to get the results of their test and, later on, to scale up the supply chain.
Lottery
Developing a vaccine, or almost any pharmaceutical, is very much like a lottery: most initial projects fail and only very few succeed. The WHO reported on 8 April 2020 that there were 78 active projects. In February 2021, there were only a handful of vaccines approved, meaning that more than 70 of those active projects have not yet been successful. At the same time, the WHO reported 182 vaccines in pre-clinical development and 73 in clinical development. In 2020, one pharmaceutical company started to develop three different COVID-19 vaccines with the hope that one of them would succeed. They made a calculated bet to focus on three, rather than on just one, or even five. Their objective was to maximize the likelihood of success by not spreading their resources too thin, nor being stuck with only one that might fail.
Traditionally, once a vaccine (or drug) succeeds, the rule of the supply chain is to consistently deliver quality products for the life of the patent – typically several years. With the flu vaccine, the role of the supply chain is to deliver a relatively stable number of doses of vaccines every year to combat the illness’s new annual strains. However, for COVID-19 vaccines, assessing the chance of success, and making investments based on a potential success or failure, has never been done in the supply chain at this scale.
The COVID-19 vaccine is a huge game changer and a brutal gambling exercise on the supply chain. The big questions last year for many companies involved in the manufacturing and delivery of the vaccine were how much capacity to build without exact figures to rely on, which vaccine would succeed (different vaccines need different manufacturing equipment) and how many doses would be needed. With time, many of these variables have changed. For example, you might remember that there was hope that after last summer that the pandemic would slowly reduce its impact – which has sadly not proved to be true.
At that time, manufacturers of vials for the vaccines, makers of syringes and many other necessary components had no idea of the volume required. Just remember the race to build respirators in spring last year (in the USA, car manufacturers switched their facilities to build respirators and they delivered approximately 80,000). Many manufacturers faced huge uncertainties regarding how many products, by when and which kind of products were needed.
Unimaginable
For supply chain experts that use processes which require production commitments of three to ten years, that was simply unimaginable. Furthermore, they had neither the management tools, practical experience nor capability to respond quickly enough. Most factory equipment requires between 6 and 18 months to be built and is expected to run for five to ten years. In the case of the COVID-19 vaccine, none of those assumptions held true. It had to be a hugely scalable supply chain created in a very short time with an uncertain lifespan; most experts expected that in less than a year the equipment would no longer be used for COVID-19 vaccines.
In spite of all these challenges, companies have responded with incredible speed and are currently delivering major quantities of vaccines. Ramping up production in such a short time on such a large scale – while making products that fulfil all the strict quality requirements needed for a vaccine – is an undeniable success story that deserves our respect and admiration.
Still, in a race against time to save lives, many feel that every minute counts – and may cost another life. This means a brutal transformation of how we manage global value chains: streamlining our decision-making processes, creating scalable chains and not being afraid of the traditional ultimate supply chain mistake – unused equipment.
Vaccine heroes
From a management perspective, there are many lessons to be learned from this success. To create scalable supply chains that take calculated risk to maximize lives saved – or, in other industries, satisfied customers – requires a fundamental rewiring of how we manage, design and evaluate supply chains. Interestingly enough, many other industries like semiconductors and medical equipment now require those scalable supply chains.
We should learn from these vaccine heroes and design new supply chains that don’t require heroic efforts to meet the needs of society.