Control towers prove their worth during coronavirus crisis
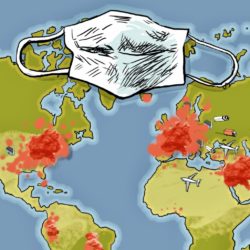
In the past couple of months, almost every supply chain has been affected by the coronavirus pandemic. Some companies have been forced to halt production, although others have been able to remain operational. Control towers, set up by 4PLs or developed by software vendors, make a real difference – even though the visibility is still far from perfect. “Do we have blind spots in our supply chain? I prefer to call it the ‘fog of war’.”
By Marcel te Lindert
The Tecniplast factory is situated in a town in northern Lombardy, Europe’s first epicentre of the coronavirus outbreak. But even during the Italian lockdown, the company was allowed to carry on with business as usual: manufacturing products for animal testing and pre-clinical studies. “We’re active in one of the vital sectors that received permission to stay open,” says Supply Chain Director Roberto Crippa during a video call. “We have of course taken all necessary precautions to comply with – or even go beyond – the government’s requirements. Our office-based employees have switched to ‘smart working’, which means minimizing their physical presence on site; they work from home as much as is possible without their job suffering. In the factory, we’ve adapted the layout of our production and assembly lines to increase the distance between operatives in order to sufficiently protect their personal health and safety.”
Tecniplast has made a conscious decision for business continuity, albeit with some reduction in production volumes. “In these uncertain times, a stop-and-go approach would have made it harder for us to maintain the necessary resilience to meet market demands. So far, it seems to be the right choice.”
Strategic inventory
Crippa describes the Tecniplast supply chain as ‘many to few’, meaning its number of suppliers is relatively large compared to the number of first-line customers: the sister companies and independent dealers who take care of sales to end customers such as pharmaceutical companies, university hospitals and research institutes. Crippa: “We make complex products that are made up of a large number of components, from plastic and steel to electronics, air technology and hydraulics. In total we use around 100,000 different parts, and a quarter of them are sourced from around 360 suppliers.” Most suppliers are based within a 250km radius of Tecniplast’s site in Buguggiate. A couple of specialized suppliers are based in the USA. “A few of our suppliers might source some products from China, but we ourselves haven’t had any problems due to the lockdown there,” states Crippa. “We’ve learned lessons from previous disruptions such as the SARS (severe acute respiratory syndrome, Ed.) outbreak. We’ve built up strategic inventory to guarantee continuity in our volatile, uncertain and complex ecosystem, so we were already prepared for a major disruption such as this pandemic.”
The buyers in Crippa’s team are in continuous contact with the suppliers to check whether they are still operational or – like so many other businesses – are halting production. That’s a tough decision for many suppliers. “If you mainly produce for companies that are now in lockdown, continuing to serve a handful of remaining customers like Tecniplast results in the loss of critical mass. In that case, it might make better business sense to stop producing altogether. We’re already noticing how important it is to have good, strong relationships with suppliers. Effective supply chain collaboration is very valuable. It can turn a risk into an opportunity, which proves that ‘risk management’ isn’t just a buzzword.”
SARS virus
Just like Crippa, the current situation reminds Jan Roodenburg of the SARS outbreak too. In the first half of 2003, 8,360 people became infected with the virus, resulting in 764 deaths. Southeast Asia bore the brunt of the outbreak. At that time, Roodenburg was working for Philips in Taiwan as Chief Operating Officer of the company’s monitor division. “To reduce the risk, we split each of our departments – from Purchasing and Logistics to Product Development and Sales – into three teams and set up a three-week shift system at different locations: working from home for one week, in one building for the second week and in another building for the third week. That way, if one team member were to become infected with the SARS virus and the whole team had to be quarantined, the other two teams could carry on working,” Roodenburg recalls. … … …
Want to read more?
Subscribe to the digital subscription to read the full version >>
or
select one of our annual or digital subscriptions to receive the next issue >>