Focus on process design
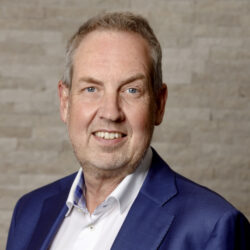
With the wave of consolidation among vendors of enterprise resource planning (ERP) systems and planning software, many supply chain improvement projects have now become more like software implementations. Central to this is that operational and decision-making processes are adapted to suit the intended software. The argument used in defence is that this makes maximum use of the software’s capabilities.
That often goes wrong. Additionally, it has now been extensively scientifically documented that, in the case of most software, only a very small number of the capabilities are utilized. That is supposedly the reason why many supply chain software implementation projects fail to achieve their intended objectives.
I recently heard a founder/CEO of one of the big retail software vendors proudly stating that in many cases they achieve inventory and waste reductions of up to 8%. But all improvements below 20% have little to do with software quality. Cleaning up data and processes can achieve similar improvements in almost all cases – even without sophisticated software. I am only impressed by algorithms and software when the actual realized benefits are more than 20%.
Knowledge of processes
The question then becomes why the redesign of processes and controls is not much more central to supply chain improvement projects. In many companies, that fundamental knowledge of supply chain and logistics processes seems to have disappeared. For example, companies no longer think carefully about where processes should be decoupled. This is so far-reaching that the time-honoured customer order decoupling point is no longer clear in many companies’ operations. In that case, the primary operational process is no longer controlled. And by ‘controlled’, I mean that after an intervention in, say, inventory levels, the service level changes predictably. Or that after a change in operational workload in the factory, lead times alter predictably.
An engineer’s perspective
During an impressive visit to Ambev South America’s supply chain headquarters in Brazil, I saw that they had chosen the route of first fundamentally designing their processes. Only then were software solutions chosen to suit the various decision-making processes. Unfortunately, at many other companies I visit, it is not the lack of software that is the problem, but the lack of a well-thought-out design of the operational and supply chain decision-making processes. We need an engineer’s perspective on the supply chain again, and we need to move away from the currently dominant software perspective.
Jan Fransoo, Professor of Operations and Logistics Management at the Tilburg School of Economics and Management