Supply chain planning is about more than the necessary processes and systems
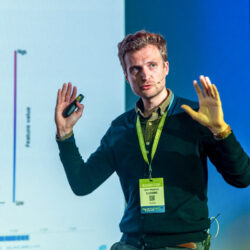
Leading software vendors showed their views on supply chain planning at the inNOWvate Supply Chain Event in Amsterdam. A pressing question that recurred in every presentation was: how do you deal with chain disruptions and erratic demand patterns? Each supplier had their own answer.
By Harm Beerens
Over the past decades, companies have spent millions of euros buying enterprise resource planning (ERP) and advanced planning and scheduling (APS) systems. But these turned out to be worthless when Covid-19 broke out. ‘As soon as there is uncertainty in the supply chain, companies quickly fall back on manually controlling their purchasing and production processes,’ observes Jean-Baptiste Clouard (pictured), CEO of the young software company Flowlity, which specializes in forecasting and inventory planning. During his presentation at inNOWvate, he advocates for a self-healing supply chain supported by three pillars: better forecasting of demand and automatic detection of deviations, being able to simulate the consequences of disruptions in real time, and automatically communicating planning decisions to all relevant supply chain partners.
Climate change
Anticipating uncertainty from within your supply chain organization better is also what Aimms does with its solutions. ‘But at a strategic planning level,’ Zoë Kokje Schouten stresses. As an example of such uncertainty, she cites the impact of climate change on a factory or distribution centre somewhere in a country. She shows a slide depicting the profitability of supply chain locations in the year 2045 for a company. Red dots indicate which locations will be at risk in terms of heat and drought. ‘Making footprint decisions is a matter of calculating scenarios and weighing up risks, sometimes for up to 20 years ahead. It’s not like our software calculates the best decision to take once; you have to repeat this process annually.’
Real-time production planning
A little later, Nazim Nachi, CEO of Planisense, a young French software company that provides solutions for demand planning, production planning, and scheduling, explains how to deal with uncertainty in a manufacturing environment. He tells his story using a case study at Bel Group. This French dairy manufacturer used Excel to control its production processes for a long time, relying heavily on its planners. Nachi: ‘It was becoming increasingly difficult to react quickly to changes in demand and last-minute changes from customers in the production sequence on the production lines. With our adaptive planning tool, which is linked to SAP and the Manufacturing Execution Systems in the factories, planning is optimized automatically and in real time. This allows Bel Group to react faster, without compromising factory efficiency.’
People are still needed
According to Reinier Zuurmond of consultancy firm Supply Chain Company, good software is definitely important, but a good planning process involves more than just technology. ‘It’s about the combination of people, systems, processes and data,’ he says during his pitch. One of the biggest uncertainties today is whether companies can find the right staff. To make his point, he describes a detailed case at food company Group of Butchers, where he and his colleagues implemented supplier Relex’s supply chain software. ‘Finding and retaining good people was one of the project’s main objectives. To reduce dependence on people, we paid a lot of attention during the project to securing knowledge in systems.’