Machine learning supports quality control in manufacturing
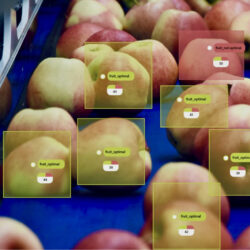
ML6 has introduced a hybrid machine learning solution for optimizing quality control in manufacturing processes. This solution combines a standardized approach with customization. According to the Belgian scale-up, which is specialized in artificial intelligence and machine learning (ML), this enables businesses to implement process optimization quickly and affordably, and increase their overall equipment effectiveness (OEE).
One key advantage of ML6’s solution is the speed with which it can be integrated. This is possible thanks to its standardized base, founded on reliable hardware and reusable building blocks. This shortens the implementation process, since time only needs to be spent on establishing communication with programmable logic controllers (PLCs), training the model and labelling the product characteristics. With the right technology, the solution can be up and running within just a few weeks.
Safeguarding quality
At the heart of the solution is a model that identifies and evaluates products and adjusts the process accordingly. This improves product quality and ensures that time, energy and resources are used more efficiently, ML6 claims. This adds value in three areas: quality control, defect removal and process control.
In terms of quality control, the high speed of many production processes makes it impossible to assess product quality manually. Thanks to technology such as computer vision and edge computing, the ML6 solution is able to check product quality thoroughly, even in the case of high throughput rates and large volumes.
Secondly, the solution achieves added value in terms of defect removal by enabling products identified as defective to be taken out of the production line. This avoids costly production resources being used on defective items and prevents defective finished products from reaching customers.
Last but not least, the solution benefits process control because the data used to check quality and remove defects also provides insight into where the most defects occur in the process. This enables the process variables to be adjusted so that production can be optimized and the number of defects can be reduced.
Customizable standard approach
This solution could be interesting for many manufacturing companies, according to Matthias Feys, Chief Technology Officer at ML6: “Quality control and process control are prone to human error, resulting in higher material losses and declining product value. Bespoke solutions are expensive and it often takes a long time before you see results. This solution can rapidly achieve the optimization that is necessary to safeguard quality and reduce waste because we already have the first phase in place.”
Although implementation is based on a standard approach, customization continues to play an important role. “With this solution, we are still delivering the customization that clients expect from us. But by offering the technology in a standardized way, we can help more companies to get the most out of their production processes, and save time and money,” Feys emphasizes.