Digital twins enable companies to continuously analyse risks
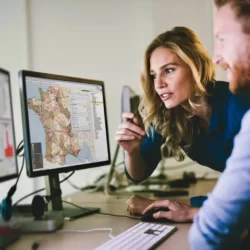
There is a seemingly endless stream of supply chain disruptions, and some factories are even at a standstill because of parts shortages and transport delays. Companies that have neglected their risk management are currently fighting one raging fire after another. During Supply Chain Media’s recent Webinar Wednesday, software supplier PSI Logistics held a number of live demos which demonstrated how digital twins can offer solutions: “Companies need to be continuously analysing a whole range of risks.”
By Marcel te Lindert
For a company with five distribution centres in Western and Central Europe, what would be the consequences if one of them were to close? Within minutes, Tim Pietrowski, Logistics Engineer at PSI Logistics, modelled this scenario using a digital twin of the distribution network. The results showed that the four remaining distribution centres would not necessarily be able to compensate for the loss. Transport costs would rise because many customers’ deliveries would have to be sent from a distribution centre located further away. And because the distances would increase, it would no longer be possible to achieve the desired service level in all regions.
Alternative distribution centre
Pietrowski then used the digital twin to explore other, potentially better solutions. First of all, he analysed the best location for an alternative distribution centre. That turned out not to be in central Germany, where the original distribution centre was, but close to Vienna instead. “This is the optimal location if we only consider the transport costs,” he said.
At this point, a real-estate broker would normally be hired to look for suitable logistics facilities near Vienna. Pietrowski said it would be wise to expand the search area beyond the borders into the Czech Republic and Hungary, since labour costs are likely to be lower there. “In this demo, the broker’s search resulted in nine possible locations: five in the Vienna area, two in the Czech Republic and two in Hungary. Analysing these nine locations using the digital twin leaves no doubt that the best location is Senica in the Czech Republic. Not only the cost level, but also the service level is clearly better than in the original situation.”
Exploring dozens of scenarios
The digital twin was created using PSIglobal which is PSI Logistics’ tool for supply chain network design. Thanks to improvements in the software’s capabilities and also the increase in computing power, it takes just a few minutes to model a complete production and/or distribution network. That enables users to ‘play around’ with the tool and explore dozens of scenarios in a short space of time. “As a result, this digital twin can be used to analyse risks,” said Cindy Schmidt, Sales Manager at PSI Logistics.
The tool is fed with datasets from the ERP, TMS and WMS, among other systems, and even Excel files to obtain the relevant information about locations, items, inventories and shipments. Once the data is available, it takes no more than a few days to build a digital twin. Schmidt: “It can then be used to design new networks and optimize existing ones. For example, what is the ideal number of distribution centres and where should they be located? How can we optimize the flow of goods in the network, and what is the associated carbon footprint? We use historical data, but can also calculate the impact of future network changes.”
Continuous analysis of risks
There is a growing need for digital twins in the context of risk analysis. Almost every supply chain manager nowadays knows how difficult it is to respond to the latest developments, let alone to achieve the company’s objectives. Businesses are struggling with a variety of issues: When should they switch from single sourcing to multiple sourcing? Which modality should they use when? How quickly can they adjust their production schedules? Should they increase their safety stocks? Schmidt: “It’s not enough for companies to tackle each issue in isolation. They need an overall view of the entire supply chain and must be continuously analysing a whole range of risks.”
Pietrowski had also prepared another case, this time relating to a company with five factories, each with a warehouse nearby. Each factory could only make one product group, which posed a major risk if the factory would be forced to close, since a complete product group would no longer be available. “The question is, what are the possibilities for improving the production flexibility while remaining cost-effective? To find out, we need to adjust the digital twin so that every product group can be produced at every location – while taking account of the different production costs per location and the start-up costs for setting up a production line,” Pietrowski explained.
Improved preparation and response
The digital twin showed that improving the production flexibility would indeed lead to higher one-off costs for the company, but that the total costs would be somewhat lower. In fact, for some product groups it would be more advantageous to produce closer to the market. The digital twin also revealed the impact if one of the factories would have to close temporarily due to a lockdown, for example. “In that case, it turns out that the total costs would rise considerably, but it would still be possible to meet customer demand with just four factories.”
If the worst-case scenario becomes reality and it’s necessary to close a factory, the company now knows, thanks to the digital twin, that it can absorb the blow. “Because the risks have been analysed and the consequences are known, the company can prepare better and respond faster. After all, the company can now fall back on ready-made solution-based strategies.”