Smart automation is more popular than full automation
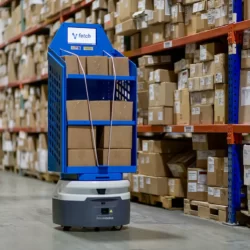
Interest in full automation for warehouses is waning, according to Zetes during the recent Webinar Wednesday. Companies are definitely still keen to invest in automating their warehouses, but are increasingly choosing a hybrid approach based on technologies that enhance employee competencies. Amir Harel, Managing Director at Zetes in the UK: “Autonomous mobile robots are flexible and scalable, and don’t require any modifications to the infrastructure.”
By Marcel te Lindert
Why are companies moving away from full automation? “Because they want to remain flexible. These are uncertain times. Companies don’t know how their business will develop in the coming years. That’s one reason why they are less willing to invest in a fully automated warehouse, plus the fact that fully automated warehouses have a major impact on the entire supply chain,” said Amir Harel.
Nevertheless, automation is still necessary. The latest technologies can help to maximize the output from the available labour, and this is becoming even more important now that warehouses across Europe are facing a worker shortage. Moreover, the growth in e-commerce is changing order profiles, resulting in smaller orders that require more manual handling. “Customers are demanding ever-shorter delivery times which is putting a lot of pressure on warehouse operations. Everything has to be done faster and faster,” explained Harel.
Autonomous mobile robots
Zetes – originally a Belgian company, but part of the Japanese Panasonic Group since 2017 – provides technology such as mobile terminals, voice systems and RFID solutions in support of manual processes. It also offers a warehouse execution system (WES) called Medea which contains the software for the smart control of its technologies. “So although Medea is definitely not a warehouse management system (WMS), it can be connected to one. We draw the line at inventory management – we don’t do that,” continued Harel.
The autonomous mobile robots (AMRs) by Fetch Robotics are a relatively new technology in Zetes’ portfolio. “These robots can work together with employees. Deploying AMRs is a flexible and scalable approach to automation, and it doesn’t require any changes to the existing infrastructure. It’s a way of improving the efficiency and accuracy of operatives.”
Hybrid automation
AMRs can be used for a variety of tasks, such as to move pallets around or to fetch racks of stock for order pickers. The Zetes managing director gave another example of their use in manual order picking processes which have up until now often been based on voice picking. “Voice picking is a simple solution that leaves the order pickers free to use their hands and eyes. Companies have been able to make considerable savings on order picking costs. But as orders are getting smaller, the walking distances are increasing and productivity is suffering.”
AMRs offer the solution. They follow the order pickers along their route past the picking locations, carrying the containers for the picked products. Each order picker is assigned their own zone to reduce walking distances, and the AMR travels from zone to zone instead. This creates hybrid automation: a mix of goods-to-man and man-to-goods processes. Harel: “Moreover, the robots boost employee satisfaction. Plus, this method of automation is scalable; it’s easy to add extra robots for peak seasons.”
A camera at the loading dock door
Harel also mentioned some other innovative uses of new technologies, such as while loading trucks. This task requires concentration because the goods must be loaded correctly in the reverse order of delivery. Terminals and barcode scanners are usually used to ensure it gets done properly. “Or sometimes RFID gates are used, but that technology doesn’t work so well with liquid products.”
An alternative is to mount cameras equipped with vision technology next to the dock doors. When an employee loads a pallet onto the trailer, the camera reads all the barcodes and labels, resulting in a faster, more efficient and less error-prone approach. “In addition, it automatically creates a database of photos that can be used as proof that all pallets left the warehouse in good condition.”
Faster than drones
Stock counting is one activity that is attracting growing attention because companies want to know exactly what they have in stock, especially if the stock information is made available online. In that case, it’s important that the inventory levels in the WMS reflect what is actually in the warehouse. “The traditional method is to count the entire stock manually, but that’s a labour-intensive, time-consuming and costly process that is only performed a few times a year, at most. The use of drones has grown in recent years, but you still need a drone operator plus an employee to keep the aisle clear.”
To tackle this challenge, Zetes has developed a vision technology-based solution consisting of a device that can be driven past all stock locations on an ordinary forklift. The device comprises wide-angle cameras that enable numerous pallets to be scanned rapidly. “As a result, a single employee can count the stock as quickly as five drone pilots could. It’s yet another example of how technology can be applied in new ways to solve existing problems.”