The Wheel of Five: Avoid overburden by managing the workload
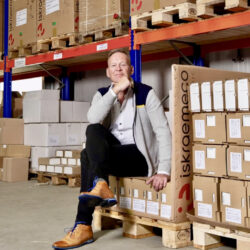
To help organizations recognize and effectively deal with good and bad variability, Involvation has developed the Wheel of Five for Supply Chain Management. This article is the first in a series of five.
If it’s no longer possible to guarantee on-time delivery, the system is overburdened. In other words, to offer delivery reliability, it is necessary to avoid overburden. In short, this can be done in two ways: by making extra capacity available and by managing the workload. Two familiar examples from everyday life are the rush-hour lane (extra capacity) and avoiding the rush hour (workload management).
Well-known examples of workload management in manufacturing are Kanban and Polca – two real-life applications of the WIPcap principle, in which work can only be allocated as long as the current work in progress (WIP) is below the agreed level. The aim is to limit the WIP in such a way that the lead time is minimized while maintaining the throughput rate (Little’s Law).
Although this sounds logical and appealing at first glance, WIPcap can come under pressure when it leads to resources with structural overcapacity running out – which is occasionally unavoidable. In that case, the noble intention to manage the workload in favour of WIP, lead time and throughput conflicts with the motto that ‘from a coverage perspective, all capacities must be fully utilized at all times!’… despite all of the late Eli Goldratt’s teachings.
Smart meter supply chain
Even today, overcapacity as a tool for avoiding overburden is not welcomed with the same enthusiasm everywhere. In fact, the aversion to overcapacity is often so great that companies choose – whether consciously or unconsciously – the path of structural overutilization. The smart meter supply chain provided a good example of this.
While transitioning households to smart electricity meters, grid operators Liander and Stedin repeatedly faced meter shortages. “This was particularly hard to believe because the installation of the smart meters seemed so predictable. A brief investigation revealed that although the installation activities were predictable, the forecasts passed to the meter manufacturers were very unreliable. Besides that, there were strong variations between the grid operators’ orders to the meter manufacturers. The cause? Classic multi-echelon inventory management resulting in the famous bullwhip effect,” says Ton Ramstijn (pictured), Project Lead Logistics at Stedin.
Bullwhip catalyst
By unconsciously presenting their suppliers with variable demand and unreliable forecasts, the grid operators had unwittingly pushed them into a planning mismatch. Faced with uncertainty and with a focus on maximum coverage and minimum working capital, the suppliers had (completely logically) opted for long lead times in order to be able to level and limited capacity in order to avoid running out. For the grid operators, this resulted in structural shortages and long delivery times: a bullwhip catalyst! “We were stuck in the planning mismatch. We needed to break through it!”
And that breakthrough came. Instead of asking their suppliers to manage their capacity based on an unreliable forecast, the grid operators now reserve production capacity beforehand based on a reliable installation plan. Furthermore, rather than having to order meters months in advance based on an unreliable forecast, the grid operators now allocate the reserved production capacity at the last minute based on the current stock of meters. Ton Ramstijn: “Our new approach has not only resulted in better availability, but also in a more straightforward process, smoother collaboration and, quite simply, less hassle.”
Read here the introduction to the Wheel of Five for Supply Chain Management.