Black swan drives demand for new technology
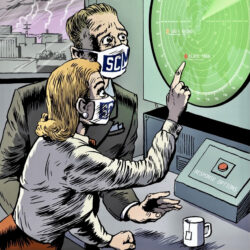
Although virologists have long warned about viruses, the COVID-19 outbreak still came as a complete surprise to the vast majority of companies. To them, it was the ‘black swan’ event that had only existed in theory in most supply chains. Now, a year later, it appears that this black swan has smoothed the way for new tech companies with innovative solutions in the areas of supply chain visibility and risk management. The need for such solutions is no longer in doubt.
By Marcel te Lindert
Thyssenkrupp Steel Europe has seven production sites in Europe. It ships the majority of the steel produced there to its European customers by road. When Europe first went into lockdown a year ago, finding sufficient transport capacity was not the biggest problem. “On the contrary: much of the demand from customers fell away,” says Torben Beyhoff of Thyssenkrupp Steel Europe. “But what was difficult was shutting down production. Our biggest problem was our rapidly increasing stock levels.”
Beyhoff is responsible for the procurement of road transport, amounting annually to around 200,000 trucks to transport a total of four million tons of steel. “We normally have around 700 trucks on the road per day. That number fell considerably during the lockdown, but even so we still had great difficulty providing our customers with reliable arrival times – especially when several countries and regions were forced to close their borders.”
Beyhoff’s team monitored the media to learn which borders were closing, and closures were often confirmed by transport companies who were stuck at those borders – although they had no idea how long for. “We had to call our customers to say that the trucks had been delayed, often without being able to say when their deliveries would arrive. That created a lot of uncertainty.”
Free access
The start-up Sixfold soon provided a solution by offering free access to its dashboard giving insight into border delays. This enabled Thyssenkrupp to issue reliable estimated times of arrival for deliveries after all – something that hadn’t been possible based on the information from its own carriers. “Large carriers with lots of trucks covering the same route knew exactly how long it had taken to cross a border on the previous day, but that was historical information. Sixfold’s dashboard was based on up-to-date information from thousands of trucks, plus it visualized the trends. It also gave us dependable data about delays at borders that we might only have to cross once a week,” says Beyhoff.
Ironically, Thyssenkrupp had started a pilot to use Sixfold’s visibility platform to gain more visibility into its transport operation in March 2020, just before the first lockdown. Beyhoff: “We had just started to connect the carriers on the main routes to the platform when the crisis forced us to put the project on hold. We restarted it earlier this year.”
More control over inbound transport
Pressure from the market contributed to this development. Having been affected by the coronavirus crisis, almost all customers have analysed their risks and concluded that they want more control over their inbound transport. “Needless to say, we’re keen to meet our customers’ needs, which is why we’ve restarted the project.”
At the time of writing, 106 of Thyssenkrupp’s 400 carriers have been connected to the platform, and more are being added every day. “The platform shows the status of the shipments they are transporting and provides accurate estimated times of arrival. The platform also enables us to give our customers insight into all transport movements to their production sites.” … … …
Want to read more?
Subscribe to the digital subscription to read the full version >>
or
This article was first published in Supply Chain Movement 40 | Q1 – 2021